The 5 Hidden Costs Bleeding Your Construction Budget (And How to Stop Them)
Discover the hidden causes quietly draining your construction budget — from poor coordination to delayed reporting. Learn how to identify and eliminate operational blind spots before they impact your profits.
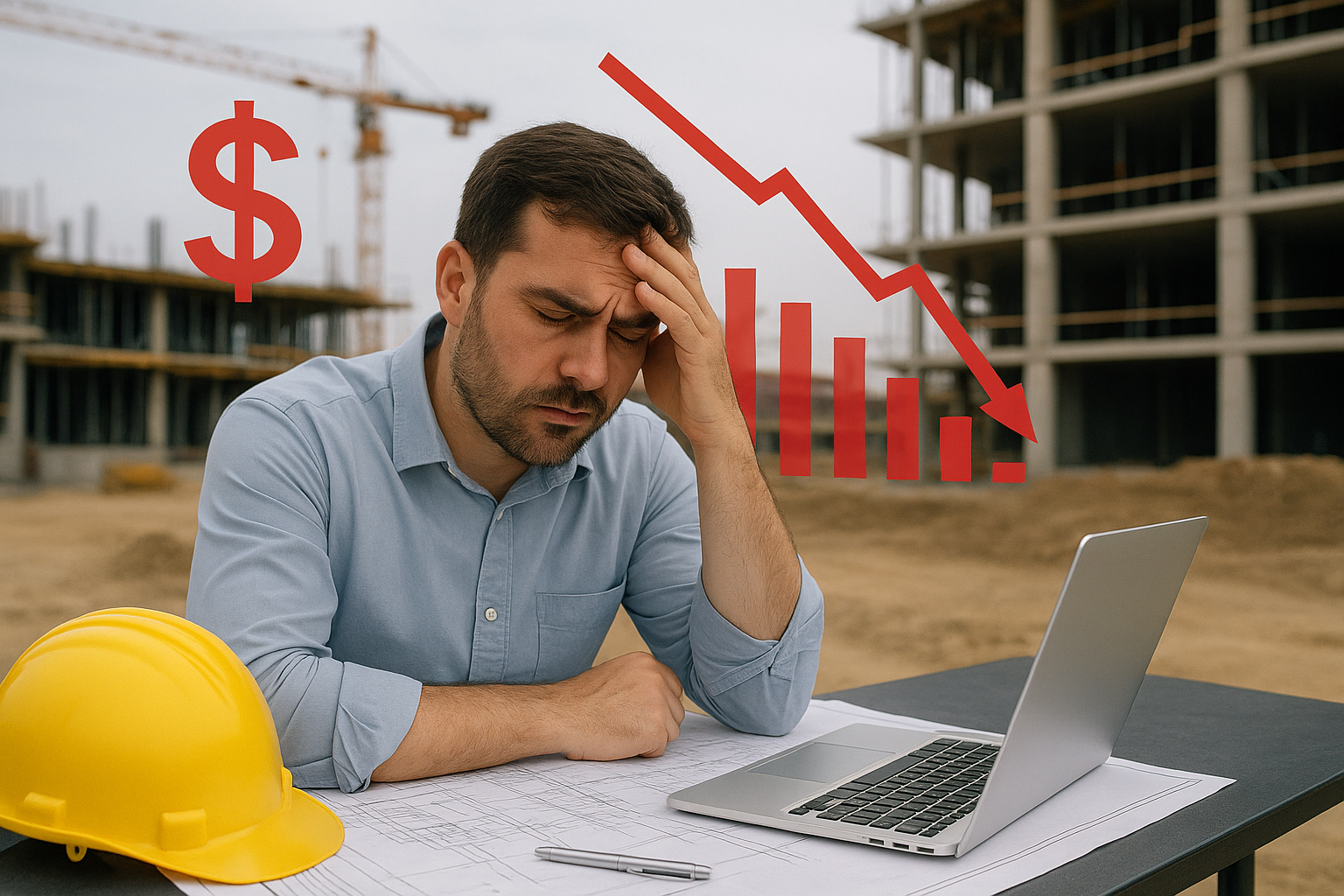
Introduction: What You Can't See Can Hurt Your Margins
Cost overruns in construction are nothing new. But what's surprising is how many of them stem not from rising material prices or labor shortages — but from operational blind spots. Delayed reporting, poor coordination, and manual processes quietly erode profitability, often without clear visibility until it's too late.
In this article, we'll uncover five of the most common hidden costs in construction management — and how to eliminate them with the right digital strategies. If your projects often run behind schedule or over budget, these may be the culprits you're not accounting for.
1. Inefficient Daily Reporting & Data Collection
One of the most overlooked contributors to cost overruns is delayed or inaccurate site reporting. When data from daily progress, material consumption, or manpower is collected manually or consolidated through scattered spreadsheets, it becomes difficult to make timely, informed decisions.
- Delays in reporting lead to reactive planning
- Miscommunication leads to duplicated efforts or missed tasks
- Inaccurate data affects forecasting and billing
How to Stop It
Implement mobile-based reporting tools that allow site supervisors to log data directly from the field. Platforms like Protrak provide live dashboards and automated daily reports — helping project managers stay updated in real time without chasing paperwork.
2. Miscommunication Between Site and Office Teams
Misalignment between field teams and back-office staff is a common operational drag. Drawings may get updated without notice, RFIs are left unresolved, and scope changes often fall through the cracks — all of which lead to rework and delays.
- Change requests don't reach the right people in time
- Site teams often work with outdated information
- RFI backlogs cause bottlenecks in execution
How to Stop It
Centralize all drawing versions, RFIs, and communication logs in a unified system. A construction management platform with drawing management and change tracking, like Protrak, ensures everyone works from the latest source — reducing the risk of miscommunication.
3. Inventory & Material Mismanagement
Whether it's a shortage of rebar or excess concrete sitting unused, poor inventory tracking can quickly lead to project delays or locked capital. Many teams still rely on manual registers or disconnected ERP entries to manage critical materials.
- Overstocking ties up resources and space
- Understocking causes unexpected stoppages
- Lack of traceability leads to theft or material loss
How to Stop It
Adopt a QR-code based material tracking system with geolocation and real-time updates. Protrak's precast and construction modules help teams monitor material usage, stockyard movements, and delivery logistics with complete transparency.
4. Reactive Quality Control
Quality checks that happen too late — or worse, after completion — are a major source of cost leakage. Rework, client complaints, and delays in approvals all add up to lost time and reduced margins.
- Defects found late require resource reallocation
- Audit processes stretch over weeks due to poor documentation
- Safety or compliance failures result in penalties
How to Stop It
Digitize your quality assurance workflows. Use predefined checklists, photo-based inspections, and non-conformance tracking integrated with corrective and preventive action (CAPA) plans. Protrak allows QA/QC teams to conduct inspections even offline, ensuring consistency and traceability.
5. Manual Handover & Snag List Processes
The final stages of a project are critical, yet often slowed down by paperwork-heavy handover procedures. Unresolved Snag list items, missing documentation, or scattered communication with clients can delay occupancy and payments.
- Extended handover timelines delay cash flow
- Snag list resolution gets lost in email threads
- Client dissatisfaction affects future projects
How to Stop It
Automate Snag list creation and tracking using mobile apps that sync with your central system. Protrak streamlines the unit handover process with digital inspections, client sign-offs, and centralized recordkeeping — ensuring a smoother, faster closeout.
Conclusion: Visibility Is the Key to Profitability
The most dangerous construction costs are not the ones you see coming — it's the hidden inefficiencies that accumulate over time. By digitizing everyday workflows and bridging gaps between teams, construction companies can gain the visibility they need to reduce delays, minimize rework, and protect their margins.
With Protrak's low-code platform, your team can deploy industry-specific workflows across planning, QA/QC, inventory, and handover — without writing a single line of code.
Want to uncover the hidden costs in your projects?
Book a demo with Protrak and start building smarter today.